Back
- Lawn & Garden
- Agriculture
- Construction
- Landscaping & Grounds Care
- Golf & Sports Turf
- Forestry
- Engines & Drivetrains
- Government & Corporate Sales
- View All Equipment
- View Used Equipment
- Parts
- Manuals & Training
- Warranty & Protection Plans
- Expert Check
- John Deere Connected Support™
- StellarSupport™
- Recalls
- Safety
- Utility Tractors (23-195 Engine HP)
- Specialty Tractors (75-155 Engine HP)
- Row Crop Tractors (145-410 Engine HP)
- 4WD and Track Tractors (390-640 Engine HP)
- Utility Tractors Attachments & Accessories
- Tillage
- Combine Harvesters
- Cotton Harvesters
- Sugar Harvesters
- Hay & Forage
- Planting Equipment
- Seeding Equipment
- Gator™ Utility Vehicles
- Gator™ Attachments & Accessories
- Loaders for Tractors
- Scraper Systems
- Sprayers
- Precision Ag Technology
- Home & Workshop Products
- Used Agriculture Equipment
- INDUSTRIAL DIESEL ENGINES
- Final Tier 4/Stage V
- Interim Tier 4 / Stage III
- Tier 3/Stage III
- Tier 2 and Lesser Regulated
- MARINE ENGINES
- Commercial/Workboat
- Recreational/Pleasure Craft
- GENERATOR DRIVE ENGINES
- Standby/Stationary
- Prime/Portable
- DRIVETRAIN EQUIPMENT
- Pump Drives
- Transmissions
- Axles
- Planetary Gear Drives
- Vehicle Electrification
- TRACTORS & MOWERS
- Ride-On Mowers
- Utility Tractors (22.4-140 Engine HP)
- Specialty Tractors (75-155 Engine HP)
- Residential ZTrak™ Zero-Turn Mowers
- Commercial Mowers
- CONSTRUCTION
- Backhoes
- Compact Track Loaders
- Dozers
- Skid Steers
- Motor Graders
- Wheel Loaders
- UTILITY VEHICLES & ACCESSORIES
- Gator™ Utility Vehicles
- Gator™ Utility Vehicles Attachments & Accessories
- ATTACHMENTS & ACCESSORIES
- Attachments, Accessories & Implements
- Home & Workshop Products
- Front-End Loaders for Tractors
- Application Equipment
- Attachments, Accessories & Implements
- Backhoes
- Dozers
- Engines
- Forwarders
- Gator™ Utility Vehicles
- Hay & Forage
- Combine Harvesters
- Cotton Harvesters
- Sugar Harvesters
- Home & Workshop Products
- Motor Graders
- Mowers
- Planting Equipment
- Precision Ag Technology
- Scraper Systems
- Seeding Equipment
- Skidders
- Sprayers
- Swing Machines
- Tillage
- Tractors
- Home
- c441r round wrapping baler euro spec
C441RVariable Chamber Wrapping Baler
- Tandem or single axle
- Premium specification
- Excellent in all kinds of crops
- Produces around 80 perfect bales an hour
C441R
Features
Features
Expand All
Collapse All
C440R sub-assembly
The C440R is a single-operator machine. While past silage making required one operator for baling and another wrapping, the C440R gathers all operations in a single place.
In order to provide the best productivity and forage quality, all baler functions are developed from John Deere operator’s well-known products:
– The bales are formed by the new F440R Baler
– When wrapped, the bales are transferred to the wrapping area by the patented Transport Table System (TTS)
– The plastic film is wrapped by a two-arm system, the same as the 900 Series wrapping baler solution.
– The overall machine is handled by a rolling frame with tandem axle.
The TTS, rolling frame, and the electric harness are specially designed for the C440R Balers:
– The component durability is aligned to have a similar wear level for the life of the machine.
– The weight of the components are optimized
– The management software maximizes overall productivity
Table in unloading position
Smooth bale handling
The bale transfer from chamber to wrapping area is a critical step in the C440R cycle. The TTS is designed to is:
– Limit stopped time
– Limit time needed to move bales to the wrapping area
– Avoid bale shape damage. Deformation can cause air pockets and spoilage.
– Limit shock transferred to the machine frame to maintain durability
– Maintain machine balance during bale transfer, even on slopes
– Provide a smooth bale unload on the ground to avoid film puncture
The TTS helps to avoid bale kick that causes shape damage and stress to the frame, and gravity transfer that causes bad bale tracking on slopes. It also uses a patented gliding table positioned under the bale chamber. The railways gently move the table to the wrapping arms, avoiding ball roll. Four wide and endless belts and four guiding rolls maintain the bale in position to allow film preservation.
Because of the smooth motion, the quantity of net required to wrap is minimized.
Wrapping system
Manual controls
The C440R features a high-performance wrapping system. The two-arm wrapping device offers:
– 750-mm plastic roll width capacity to provide a fast wrapping cycle
– 70 percent pre-stretching setting to limit film consumption and increase forage quality by avoiding air pockets
– High rotating speed up to 35 rpm.
– Proportional valve and film breakage sensor as a base to provide a constant wrapping quality no matter the film breakage or end of roll.
– High-efficiency safety system to stop the wrapping process in case of interfere with a turning satellite
– Emergency circuit-breaker shutting all hydraulic and electrical functions
– Manual controls located close to the wrapping device, allowing easy maintenance and fast plastic roll replacement
– 12-roll autonomy for continuous uptime
Variable table speed profile
Variable arm speed profile
By managing the C440R subassembly design, John Deere is able to maximize overall productivity. A few details that impact the C440R performance are:
– The table does not wait until the end of the tying process to reach the unloading position. Nearly five seconds after beginning of the tying process, the wrapping table automatically reaches the right position to minimize stopping time.
– The table speed varies pending on position and the speed, not compromising the bale stability. The table accelerates during the first centimeters and decelerates in the last centimeters.
– The wrapping arm speed also varies based on cycle status. In order to avoid downtime caused by film breakage during the arm launch, the arms gently accelerate during the first rotation while speed decreases during last turn to provide a high-quality film cut.
Bale tilt
Rubber mat
Steep-slope kit
Working light
In order to boost baler versatility and efficiency, several options can be added to the C440R wrapping device :
– A bale tilt allows the film wrapped bales to unload flat, which results is lower film puncture risks reduced bale rolling risk, and time saving for handling.
– A rubber mat provides smooth bale unloading and reduces film puncture, especially with alfalfa or when dumping in automatic mode.
– A steep-slope kit increases baling capacity in hilly conditions. A roll located on the rear of the wrapping table prevents bales from dropping..
– A working light illuminates the wrapping area. Plastic roll changing is fast and easy even when baling by night.
Dumping mode choices
Grouper mode
Depending on the crop type or field conditions, changing the dumping mode can significantly impact productivity, forage quality, and overall safety. For example:
– When baling silage alone in a flat field, the automatic dumping mode provides maximized productivity.
– When baling silage alone in hilly fields or during demonstration, the manual dumping mode offers increased safety and avoids accidental unloading of bales.
– When baling alfalfa, dumping while the baler is stopped to avoid film puncture.
– When baling hay or straw and not using plastic wrap, grouping two bales limits handling time.
All of these functions and dumping mode can be selected from the monitor.
Large-diameter stripper and five teeth bars improve picking capacity
The C440R Baler uses the same, highly-productive and efficient pickup of the 900 Series Variable Chamber Balers. To fit all conditions, the baler is available with 2.0-m (1.86-m DIN) or 2.20-m (2.12-m DIN) width.
The pickup features five tines (four on the F440M) bars with a low-rotating speed. The large-diameter strippers allow five tines bars in the pickup instead of four on the previous series. The picking capacity is increased by more than 10 percent. While picking capacity is increased, the rotating speed decreases by 12 percent. With bearings added to the cam track, all of these features provide a smooth and quiet ride with extended uptime.
In addition to the high spec features, the C440R benefits from stainless steel strippers, a market exclusivity. Stainless steel provides the following advantages:
– No rust
– Constant gliding capacity
– High-resistance to aggressive additives such as propionic acids
The C440R Balers pickup uses the cam track design. The cam track design provides a better quality solution when harvesting wet crops. Contrary to the cam-less design, the cam track pickup:
– Features a short space between the tines and rotor, limiting dead zone.
– Avoids pinching area, so no crops are plugged into the pickup drums.
Maxicut™ HC 25 has a single axis for rotor and converging augers
Maxicut™ HC 25 has a single axis for rotor and converging augers
In order to maximize productivity in the toughest swaths, the C440R Baler features a HC rotor design. Converging augers are aligned with the rotor, limiting the free space between pickup teeth and rotor. Plugging risk is also decreased and crop transfer is highly improved. The simple HC rotor design also reduces the number of moving parts and provides reliability. For example, stress on the rotor is distributed along all of the rotor and overhang load on the bearings is avoided.
The C440R is only available with a precutter, offering space between knives as short as 40 mm or 80 mm.
Double-heat treatment for concise cut and long life
Individual knife security for quality forage
The C440R Balers are efficient in baling a high amount of cut silage. The Maxicut HC 13 and Maxicut HC 25 feature exclusive high-quality knives, providing several advantages:
-Bulk heat treatment to reduce risk of knife breakage.
-Surface heat treatment of the cutting area to provide better cutting quality and knife durability.
Knive sets from the cab with Maxicut HC 25
The C440R can be used on several kinds of crops, in which knives can be engaged or removed. No matter the rotor type or monitor, this operation is easily managed from the cab.
When using the Maxicut HC 25 precutter, crops can be cut as short as 40 mm, but only half of the knives can be engaged. This system proposes to use two different sets of knives for the same cutting width, to allow the use of sharp knives longer. By using sharpened knives versus blunt, fuel consumption can be decreased by up to 10 percent.
Drop floor covers rotor full width
Parallel kinematics avoids narrowing
No matter the operator experience, plugs can still occur, especially with large silage swaths. The C440R is equipped as a base with a drop floor unplugging system. Same as the 900 Series Balers, the F440R drop floor features exclusive advantages:
– Full width design – by covering the full pickup width, the device is able to remove plugs, even located under converging augers.
– Parallel kinematic – no rear or front hinge means no narrowing. The C440R drop floor offers a constant 40-mm free space through the feeding channel when activated. This is enough to decompress the crops and avoid crop loss.
No matter the precutter or monitor type, the drop floor unplugging system can be easily managed from the cab.
Three-lip plastic seal
Fully greased bearings
In order to provide high-quality rolls, the F440R rolls are not two half shelves welded together. John Deere only uses tubes that are ribbed to better grip the crops. The dedicated manufacturing process produces an accurate cylindrical shape, avoiding vibration.
All rolls benefit from greased bearings on both sides, not only on the chain side. A three-lip plastic seal locks off debris, silage juice, and moisture from bearings.
Inner reinforcements carry highest load
Red rolls are reinforced and blue rolls are HD
Depending on their positions, the rolls do not all carry the same load and stress. Some rolls feature specific reinforcements, providing extended reliability:
Easy bale size adjustment
Independent density setting
The balers allow operators to maximize the quantity of material or minimize due to shipping and storage needs. The bale diameter can be easily adjusted from 1.25 m to 1.35 m (4.10 ft to 4.43 ft) by gliding a skid. The continuous settings allow an accurate and quick choice. The bale diameter is controlled by contactless sensors, which provide long durability and error proof monitoring.
The bale density and size are not directly linked on the F440R and C440R Balers. Depending on the crop type, operators can independently choose a small-diameter bale with high density, a 1.30 m (4.27 ft) with large density, or large diameter with low density. A pressure gauge located on the front of the baler communicating the density is linked to the density harness. The density is easily adjusted by a knob located on the front black grid. No tool is required.
The density harness is a closed and isolated circuit, meaning that there is no continuous oil flow requiring extra power consumption.
Exclusive concept increases machine durability and forage quality
Integrated solution optimizes weight and performance
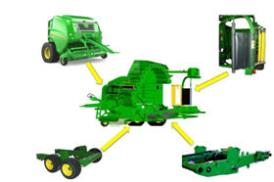
TTS offers smooth bale transfer
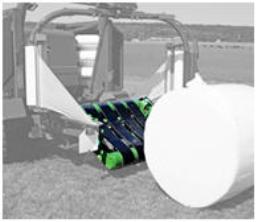
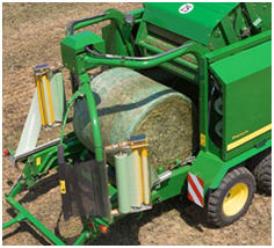
High-speed wrapping arms increase overall productivity
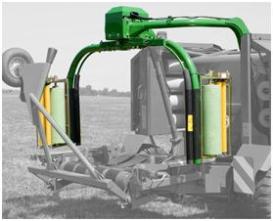
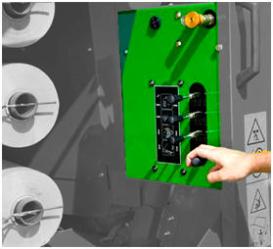
Optimized cycle management increases productivity
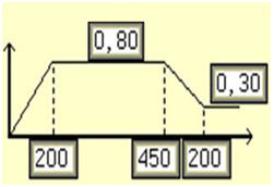
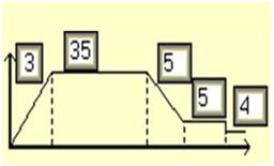
Options boost machine versatility
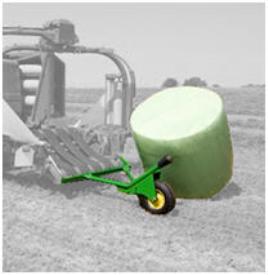
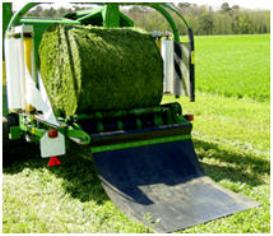
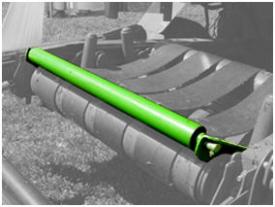
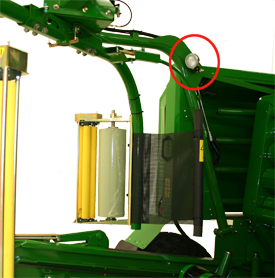
Wide-choice of dumping modes enhance efficiency, forage quality, and safety
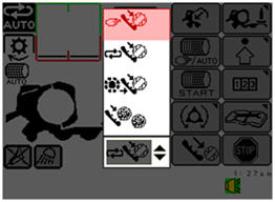
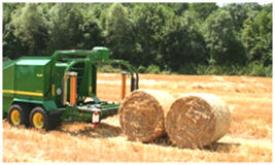
High-capacity feeding system boosts productivity
New pickup design improves capacity and durability
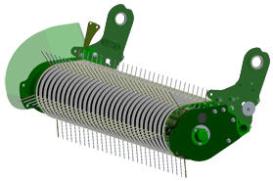

High-capacity (HC) rotor for higher productivity
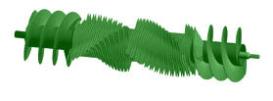
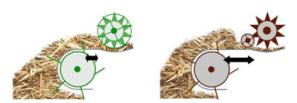
Maxicut HC 13 |
Maxicut HC 25 |
|
Number of knives |
0/13 |
0/12/13/25 |
Space between knives |
Full crop length 80 mm |
Full crop length 40 mm 80 mm |
Best use |
Silage, hay, straw |
Silage, hay, straw |
High cutting quality provides better forage
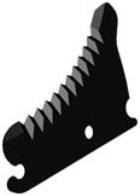
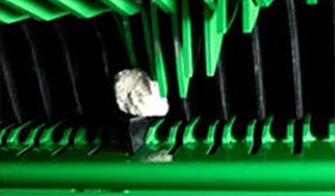

Select number of knives from the cab to increase uptime

Drop floor can remove the worst plugs
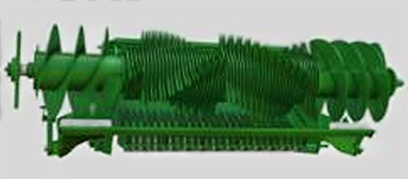
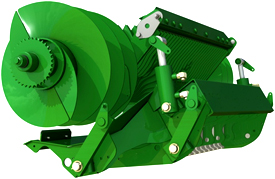

Heavy-duty (HD) bale chamber provides density and durability
Rolls manufacturing provides long lifespan
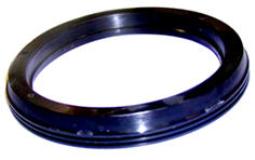
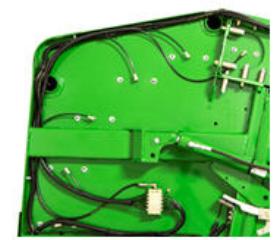
Specific rolls handle the stress
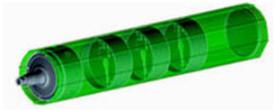
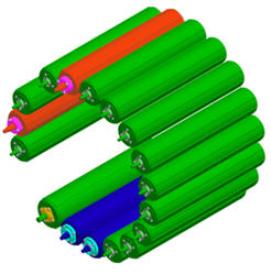

- Rolls numbered 14 and 17 transmit the load of the main drive to the secondary chains (front bale chamber part and tailgate). Due to this specific stress, both rolls feature an inner reinforcement (bell shape) on the left-hand side.
- Rolls numbered 10 and 11, located on the bottom, sustain the weight of the bale. To carry heavy loads, both rolls have three inner reinforcements in addition to the bell on the left-hand side (same as rolls 14 and 17).
Adjust bale size and density independently
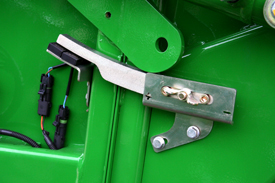
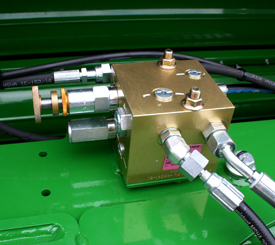
Offers and Discounts
Related Products
Product Information & Support
You May Also Be Interested In
Product features are based on published information at the time of publication. Product features are subject to change without notice. Contact your local John Deere dealer for more information.